Scaling is a very common problem in the pulp and paper industry that disturb some processes that can result in large production losses and considerable increase in maintenance costs. In the last decades due to environmental and government regulations most mills minimized their effluent discharges and applied some modifications (i.e., re-circulations) in their systems. Since water usage is a big concern, mills recirculate their water from one stage to a different one (i.e., oxygen delignification to the brown stock washers) but this new procedure changes the chemical conditions of the latter stage. A metal can be in solution during a stage “A” (i.e., sourcing stage), but it may come out of solution (i.e., precipitate) in a stage “B” (recipient stage) due to an unfavorable pH.
Scaling takes place almost everywhere in a kraft mill, for example, in digester heaters and evaporators (Duggirala 1994), bleach plants (Shevchenko and Duggirala, 2009), dissolving tanks, green and white liquor lines, slaker and causticizers, and paper machines. The most common deposits in the Kraft recovery cycle are calcium oxalate, barium sulphate and calcium carbonate. See Figure 1.
Rudie and Hart (2012) stated that “Understanding scale problems requires an understanding of the state of the metals entering the process stage and the chemistry of the stage where the scale forms”.
This paper examines general aspects of deadload, scale depositions in a kraft pulp mill, calcium carbonate (i.e., CaCO3) depositions on continuous digesters (i.e., liquor heaters), the factors that accelerate its deposition and scaling control strategies.
Calcium in wood - Calcium (Ca++)/Calcium Carbonate (CaCO3)
The most common source of calcium (i.e., Ca++) during kraft pulping is wood (Vegunta 2023, Felissia et al., 2007) followed by white liquor (Felissia et al., 2007). As per Vegunta (2023), the calcium that is released from the wood at the beginning of the cooking is mainly soluble in the black liquor before reacting with carbonate (i.e., CO3=) to form calcium carbonate. The scaling of calcium carbonate is due to high calcium ion (Ca++) and carbonate (CO3=) concentrations together with high alkalinity and temperature levels (Felissia et al., 2007, Banerjee (2012). According to Ulmgren (2005), most of the carbonate ions are introduced into the digester together with the white liquor and by formation during pulping and oxygen delignification.
Common sources of scaling in kraft pulp mills
Most of the metals participating on scaling issues in a kraft pulp mill are the result of metals coming with the incoming wood or inefficiencies of particular processes (i.e., recausticizing efficiency, reduction efficiency) or metals present as impurities in the make-up chemicals to replace chemical losses. The main sources of these depositions are given in Figure 2.
eadload Origins
As per Grace & Tran (2009) the main dead load chemicals are sodium carbonate generated from incomplete conversion during causticizing and sodium sulfate from low reduction efficiency in the recovery boiler. Additionally, as per Greer (1999), scaling during pulping and bleaching operations is due to factors like pH and temperature shocks, severe mechanical or hydrodynamic shear forces and supersaturation of scaling ions.
The chemicals used in the digester are recovered in the 97% - 98% range. Most of the sodium sulfate (Na2SO4) is reduced to sodium sulfide (Na2S) in the recovery boiler at reduction efficiencies around 90% - 94% and the sodium carbonate (Na2CO3) is converted to NaOH in the causticizers with recausticizing efficiencies in the range 80% - 84% (Tran and Vakkilainnen, 2016), Green and Hough (1992). See equations 1 and 2. Approximately 20% of the recovered inorganic chemicals that recirculate through the recovery system as inactive species are referred as “dead load” chemicals (Grace and Tran, 2009).
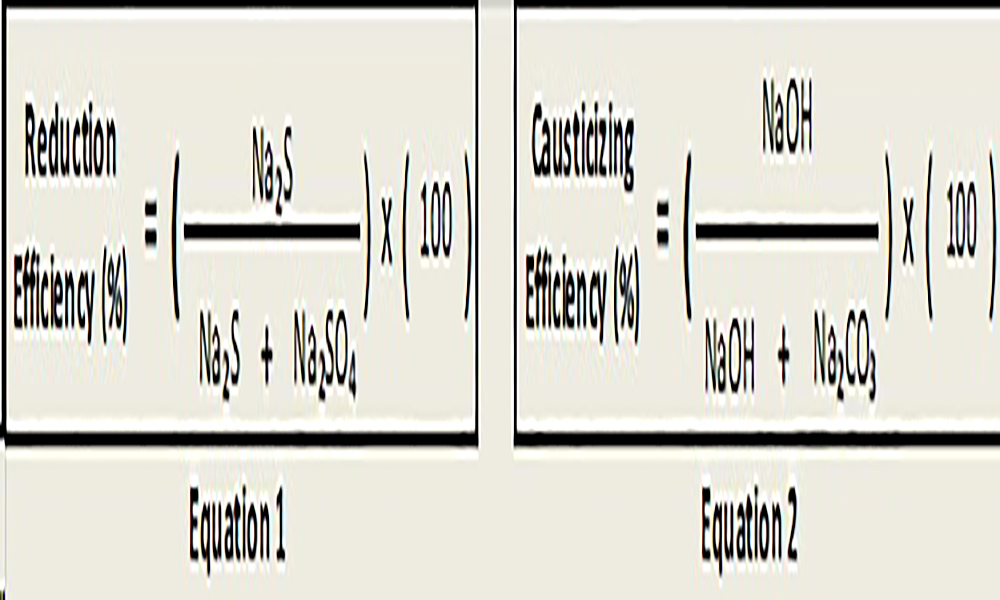
As per above, reduction efficiency and causticizing efficiency, not all of the Na2SO4 is reduced to Na2S nor all the Na2CO3 is causticized to NaOH, and therefore some sodium sulfate and sodium carbonate recirculate in the system. Furthermore, other compounds like sodium thiosulfate (Na2S2O3), sodium sulfite (Na2SO3), sodium chloride (NaCl) and a set of chemicals known as “non-process elements” (i.e., K+, Al3+, Mg2+, Mn2+, Cl-, etc.) together constitute the dead load material (Grace and Tran, 2009). The most common sources of dead load in the kraft recovery cycle are presented in Figure 3.
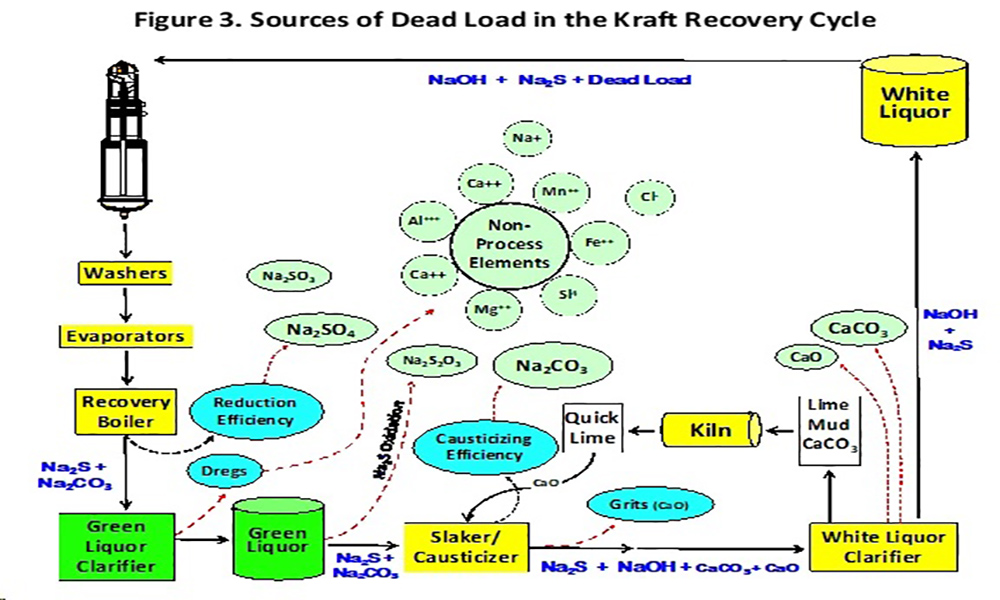
Calcium carbonate has an affinity for dregs in the white liquor producing a less dense (i.e., slower settling) particles in the white liquor. This condition results in calcium carry-over that contributes to digester and evaporator scaling problems. The slower settling also reduces the mud washing efficiency that results in more soda and water being sent to the kiln that can lead to an increase in balls and rings, total reduced sulfur (TRS) emissions and fuel consumption (Bajpai 2008).
Effects of deadload and scaling deposits in a kraft mill
High levels of deadload in a kraft mill affect the functioning of some equipment, pipelines and pumps with process and economic consequences. The most common effects of deadload in a kraft mill are: 1) increased energy usage (i.e., heating extra water), 2) greater chemical losses, 3) scaling deposits reducing equipment capacity (i.e., evaporators due to higher boiling points, digesters, dissolving tank, etc.), 4) downtime for cleaning operations, 5) lost production, etc. (Grace and Tran, 2009). In general, scale deposits in kraft mills include complexes of calcium (carbonate, oxalate, sulfate, silicates), aluminum (silicates, hydroxides, phosphates), barium sulfate and silicates of magnesium, etc. (Sitholé 2000).
Deadload reduction
Kraft mills can reduce their deadload by: 1) reducing sodium carbonate (Na2CO3) by increasing causticizing efficiencies; 2) reducing sodium sulfate (Na2SO4) by increasing reduction efficiencies; 3) minimizing chlorides by reducing chloride inputs or purging it (i.e., precipitator dust), and 4) improving process control measurements at the white liquor plant, etc. The largest contributor of deadload is sodium carbonate. Increasing causticizing efficiency reduces more the deadload than increasing the reduction efficiency as 1% increase in causticizing efficiency decreases the deadload by 6-7 kg/mtp while a 1% increase in reduction efficiency decreases the deadload by 2-3 kg/mtp (Grace and Tran, 2009). The two most important variables to determine the effect of deadload reduction are the Causticizing Efficiency (CE%) and the Reduction Efficiency (RE%) (Chandra 2004). The primary benefit of reducing the deadload is in energy savings in the digester, evaporators and recovery boiler (Grace and Tran, 2009). Most common purging ways for calcium ions are with the green liquor dregs as (CaCO3) and with the pulp and the bleaching effluents (Ulmgren 2005).
Inverse Solubility Behaviour of calcium carbonate
Most chemical compounds in solution increase their solubility when the temperature increases; however, a few compounds (i.e., CaCO3, Mg(OH)2, CaSO4) shows the opposite behaviour that turn these compounds less soluble (i.e., precipitate out) when the temperature increases (Felissia et al., 2007). This phenomenon is known as “inverse solubility” with temperature (Severtson et al., 1999).
Scaling in Continuous Digesters
The most common areas prone to scaling are the chip chute, top separator, liquor heaters, and cooking and extraction screens. Scaling deposits in heaters and screens are easily noticed as they severely impede the cooking liquor flows (Greer 1999). Scaling rates can be monitored by using process variables such as liquor flows, temperatures, and heat-transfer coefficients (Severtson 1999).
When calcium carbonate precipitate in the digester heaters, the heat transfer of these units goes down and the digester operators react by increasing the temperatures on the heaters. This higher temperature favours the inverse solubility behaviour of CaCO3 and higher scaling problems will occur on the heaters. Then, mills using poor white liquor quality (i.e., high deadload - CaCO3) will aggravate this scaling situation even more.
Most of the calcium carbonate coming with the white liquor precipitate when heated at the high cooking temperatures in the digester (i.e., liquor heaters). To avoid downtimes most continuous cooking digesters has an extra liquor heater that can be out of service for cleaning (i.e., acid cleaning) without impacting the mill production.
Scaling in continuous cooking digester has the following effects: reduces pulp mill productivity, reduces the efficiency of the pulping process, forces to costly cleaning of equipment, increases the steam usage, reduces liquor flow rates, forces to unscheduled downtime, etc. The most frequent deposit on continuous digesters (i.e., heaters and extraction screens) is calcium carbonate. Scaling of heat exchangers results in increased steam usage and reduction of the liquor flow rates that result in Kappa number variability and increase carryover of pulping chemicals (Severtson et al., 1999).
The main factors that affect scaling in continuous digesters are inverse solubility, increase of liquor flows, higher cooking temperatures, white liquor calcium carbonate (CaCO3) content, Ca++ content in wood, carbonates (CO3=) in the cooking liquor, high alkalinity, etc. See Figure 4.
Digester Scale Control Strategies
These strategies have been divided into two categories: preventive and removal methods. The preventive methods include the chemical and process control treatments while the removal group includes the chemical and mechanical treatments. See Table 1.
Chemical preventive treatments: Antiscaling agents, sequestrants, lignin derivatives
When using the term “prevention” it refers to a reduction in scaling rates rather than a complete elimination of the routes to generate the deposits. An antiscalant agent interrupt or interfere the mechanisms for the formation of crystalline deposits. Both antiscalant or sequestrants have been used to prevent scale depositions.
According to Väisänen 2011), scaling problems in kraft continuous digesters can be eased or solved by using chemical additives referred as antiscalants or scale inhibitors. Examples of common scale inhibitors were referred in the chemical groups of the phosphonates and the polycarboxylates.
Most antiscaling agents belong to different chemical groups such as polyphosphates, phosphate esters, phosphonates [i.e., 1-hydroxyethylidene-1,1-diphosphonic acid (HEDP); diethylene triamine pentamethylene phosphonic acid (DTPMPA)], lignin derivatives, polyacrylates, carboxylate polymers, etc. Most anti-scaling agents work by one or more of the following three mechanisms: threshold inhibition, crystal dispersion and crystal modification (Severtson 1999).
Common antiscalant feedpoints in a continuous digester are: a) suction side of the chip chute pump, b) BC (bottom circulation) loop and c) after the digester liquor heater (Duggirala 1994).
Using an anti-scaling program allows a kraft mill to use their digesters without serious scaling issues by extending the scale-free periods to 2-6 months. Some suppliers sell their products by ensuring scale-free periods of 1 year or more but this depends on many factors like white liquor quality (i.e., CaCO3 levels), liquor flows through heaters, cooking temperatures, etc.
Sequestrants or chelants are chemicals that form soluble complexes with dissolved calcium preventing the formation of CaCO3 deposits. Some examples are ethylenediaminetetraacetic acid (EDTA), diethylene triamine pentaacetic acid (DTPA), etc. According to Banerjee (2012), calcium carbonate (CaCO3) is generated from the reaction of calcium from wood with carbonates (CO3=) in the cooking liquor. He proposed using lignin derivatives as antiscaling agents due to their ability to chelate calcium by adding 1% black liquor to white liquor.
When using EDTA acidic conditions are required, while DTPA function on strong alkaline conditions like kraft pulping (Felissia and Area, 2004). As per Li and Tschirner (2002), the hydroxyethylidene diphosphonic acid (HEDP) and diethylenetriamine pentamethylene phosphonic acid (DTPA) can be used as chelating agents in kraft pulping.
Process Control preventive treatments: Temperature control, Liquors flow control, Calcium filtration, thermal deactivation
According to Duggirala (1994), in the past 50 years or so, the process control treatments have been preferred over the chemical preventive treatments. Both temperature control and liquor flows control can minimize scale depositions.
Thermal deactivation has been proposed to minimize the scaling tendency of calcium in the cooking liquors. This calcium deactivation has been practiced in some digesters (Jiang and Hill, 2007).
A combination of process control and chemical control prevention treatments should provide the best strategy to impede scale formations (Duggirala 1994).
Removal treatments
Chemical removal treatments
The most common removal chemical treatment is the acid cleaning (i.e., sulfamic acid). Removing most scaling deposits is a very expensive cleaning operation because it includes, not only the cost of the chemicals but also the costs associated with personnel, effluent disposal, acid cleaning wears, corrosion of the equipment and in most cases the needed unscheduled downtime that equates in lost production.
It is worthy to mention that off-line acid cleaning can be used frequently to de-scale the digester heaters; however, the removal of deposits inside the digester must be done once or twice a year during a routine shutdown.
Mechanical removal treatments
The removal (i.e., cleaning) mechanical treatments such as steam shocks and hydroblasts have been used effectively to remove mineral deposits (Severtson 1999). Hydroblasting is a mechanical process that includes high-pressure water to remove scale deposits.
An interesting difference between preventive and removal methods is that the removal option forces to unscheduled downtime with inevitable lost production.
Final Remarks
Almost all kraft pulp mills have the optimal conditions (i.e., pH, high alkalinity, carbonate concentrations and supersaturation) for the scaling of calcium carbonate to take place in many parts of the whole kraft system (i.e., green liquor lines, digester liquor heaters, etc) (Severtson 1999).
The CaCO3 concentrations in the kraft cycle are high and its scaling is found at different degrees in the whole system. In the case of the liquor heaters, once the scaling takes place at these locations, these depositions inhibit the cooking liquor flows forcing the operators to increase the liquor flows and temperatures to counterbalance the flow issue. Additionally, if using poor white liquor quality (i.e., high calcium carbonate content) at higher temperatures (i.e., inverse solubility) then more CaCO3 will precipitate in the heaters.
It seems that the ideal scaling control strategy should include the following steps: 1) Minimize the deadload levels, 2) Improve the white liquor clarification, 3) Search for the correct scaling prevention and/or removal treatment, 4) Find the correct feed points and dosage of chemical applications (i.e., antiscaling agents), 5) Study the factors (i.e., inverse solubility) affecting scaling in continuous digesters (I.e., liquor heaters), etc.
Source:https://www.paperadvance.com/