آنچه که فلکسوگرافی را از دیگر روش های چاپی متمایز می کند، استفاده از کلیشه منعطف با برجستگی هایی در نواحی چاپ شونده است. این کلیشه پس از سوار شدن بر سیلندر، مرکب را از طریق تماس با نوردی به نام آنیلوکس دریافت می کند. نورد آنیلوکس در اصل یک سیلندر تماماً حکاکی شده بود که به صورت مکانیکی تا عمق لایه مسی حکاکی و سپس با پوششی از کروم سخت آبکاری می شد. این روش تا آنجایی که به چاپ متون ختم می شد، کاربردی و مناسب بود. اما از دهه 1990 که چاپخانه داران به پتانسیل های این روش پی بردند و صنعت بسته بندی تحت تاثیر صنعت لیبل زنی مواد غذایی قرار گرفت، اجزای فرایند فلکسوگرافی به گونه ای تصاعدی بهبود یافت. پیشتاز این اجزا، نورد آنیلوکسبو که دیگر از جنس سرامیک ساخته و با لیزر حکاکی می شد. از آنجایی که هر نورد آنیلوکس برای کر با انواع و تعداد زیادی کلیشه ساخته می شد، سازندگان آن می بایست سطوح حکاکی شده را با عمر طولانی تری تولید می کردند. به این ترتیب ابتدا حکاکی مکانیکی مس و کروم سخت به دیگر فلزات (مانند فولادهای نرم و ضد زنگ) تغییر کرد و بلاخره لایه کرومی با یک پوشش سرامیکی، از طریق اسپری حرارتی جایگزین همه روش ها شد.(شکل1)
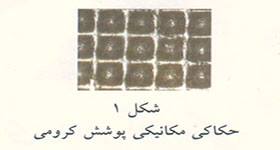
در اواخر دهه 1980 یک لایه سطح جدید برای آنیلوکس تولید شد، که با استفاده از لیزر و صورت کامپیوتری حفره هایی با الگوی مشخص در پوشش سرامیکی اسپری شده (Cr203) ،ایجاد می کرد. این گونه بود که نورد آنیلوکس با حکاکی لیزری پا به عرصه گذاشت و از محدوده 550 ترام با حکاکی مکانیکی به 2000 ترام در اینچ با روش لیزری رسید. امروز نوردهای آنیلوکس با حکاکی لیزری (Laser Engraved Ceramic-LEC) ،به عنوان با ثبات ترین ابزار تنظیم ضخامت لایه مرکب بر سطح چاپ شونده و حفظ دنسیته رنگی مطلوب شناخته شده اند.
به کار بستن نوردهای LEC در پوشش دهی گراور مستقیم
با بوجود آمدن نورد LEC، روند بهبود روش ها و تجهیزات به سوی افزایش دنسیته سطح سرامیک، بهبود در پرداخت سطح و ایجاد تنوع در هندسه حفره ها سوق پیدا کرد. همچنین اکنون با آخرین پیشرفت های لیزر فیبری 500 وات، سازندگان نورد آنیلوکس می توانند ترام های خطی تا حد lpi20 را با ثبات کافی در دیواره و ظرفیت هایی تا 10bcm (بیلیون میکرون مکعب) را حکاکی کنند. چنین پیشرفت هایی همچنین باعث شده که نورد LEC اغلب بیشتر از سیلندر گراور در پوشش دهی و لمینیت مورد استفاده قرار گیرد. از مهم ترین مزایای اکسید کروم، ضخامت پوشش دهی آن است. Cr203 در فرایند اسپری حرارتی که در آن پود گرانول شده به میزان نیاز پاشیده می شود، پوشش با ضخامت معین را تشکیل می دهد. بنابراین تمام لایه حکاکی شونده از جنس سرامیک خواهد بود. این مزیت باعث می شود که سازنده نورد، میزان سختی یکسانی در تمام طول فرآیند حکاکی در پیش داشته باشد و نه مانند حکاکی مکانیکی که کروم سخت تنها تا عمق 0005/0 تا 002/0 اینچ از حفره های حکاکی شده حفاظت می کرد.
می توان سیلندرهای حکاکی شده به روش قدیمی را نیز با سطح LEC حکاکی مجدد کرد. برای این منظور، ابتا پس از جداسازی پوشش های قدیمی، سیلندر فولادی را با روش اسپری حرارتی اکسید کروم پوشش می دهیم. اکسید کروم حداقل 005/0 اینچ ضخامت پیدا خواهد کرد. مزیت اصلی این سیلندرها عمر طولانی آنها به میزان 10 تا 20 برابر سیلندرهای سنتی است.
مزایای سیلندرهای LEC د چاپ گراور
یکی از بزرگترین مزیت های LEC ، مقاومت آن در برابر سایش در تماس با تیغه های فولادی یا کرومی داکتر، پیگمنت های ساینده مانند اکسید تیتانیوم و همچنین سطوح ساینده در چاپ گراور مستقیم است.
مقاومت در برابر سایش، کاربرد دیگری نیز برای سیلندرهای LEC فراهم می کند. این سیلندرها می توانند در سیستم های پوشش دهی که حرکت سیلندر معکوس جهت تیغه است، بازدهی خوبی از خود نشان دهند. در این سیستم ها یکپارچگی ضخامت در پوشش دهی تنها با ظرفیت حفره ها کنترل می شود و تحت تاثیر زاویه تیغه قرار نمی گیرد. سیلندرهای LEC در انواع فرایندهای گراور قابل استفاده هستند، به ویژه در مواردی که وزن پوشش دهی در تیراژهای بالا اهمیت پیدا می کند.
انواع روش های حکاکی LEC
از آنجایی که هندسه ی حفره های حکاکی شده در سیلندرهای LEC در نرم افزار لیزر تعیین می شود (و نه توسط ابزار مکانیکی یا استایلوس)، تنوع طرح های آن می تواند بی نهایت باشد. بنابراین سطح سیلندر می تواند در هر شکل و هندسه ای حکاکی شود. این نرم افزار همراه حسگرهای خطی و حسگرهای رول می تواند دقت بسیار بالایی برای اشعه لیزر به وجود آورد.
در این سیستم، شکل چهارگوش 45 درجه ای که در روش مکانیکی حکاکی می شد، به آسانی با یک هشت ضلعی 60 درجه جایگزین شد که در آن تعداد حفره ها 15 درصد افزایش یافت. ایجاد حفره ها 15 درصد افزایش یافت. ایجاد حفره های بیشتر در یک سطح باعث کاهش حجم دیواره ها و کمک به پوشش دهی یکپارچه تر می شود. هندسه حکاکی می تواند به صورت اشکال بسته در زاویه های 45،30 یا 60 درجه، یا به صورت الگوهای متصل به هم در زوایای 70 تا 75 درجه و همچنین به صورت اشکال باز مانند خطوط باریک مستقیم باشد.
تطبیق هندسه LEC با نوع پوشش دهی
برای انتخاب بهترین هندسه حکاکی برای کاربرد در پوشش دهی، نیاز است که تا اندازه ابعاد دانه های پیگمنت و ویسکوزیته مرکب در نظر گرفته شود. برای یک پوشش نازک، هندسه حفره های آنیلوکس باید به صورت اشکال بسته باشد. در مورد پوشش های ضخیم نیز حفره هایی با اشکال باز مناسب هستند زیرا مانع از تشکیل حباب هوا در حفره ها پس از تخلیه مرکب خواهند شد. تصاویر سه بعدی در شکل 2 نشانگر چگونگی تاثیر حجم و تعداد خطوط حکاکی شده در شکل هندسی حفره ها است. دیواره های حفره و کف آن، در یک ترکیب صحیح می توانند به صورتی شکل بگیرند که به تخلیه مرکب یا ماده پوشش دهی از حفره ها و همچنین به شست و شوی آنیلوکس کمک کنند.\
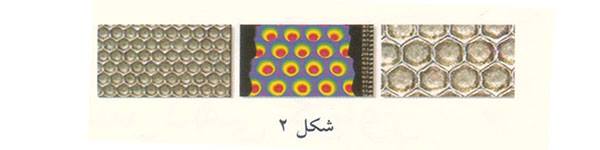
سرامیک مقاومت بالایی در برابر سایش دارد، به همین دلیل تیغه های داکتر با عمر طولانی تری قابل استفاده خواهند بود. اگر چه از طرفی، سرامیک مقاومت کمی در برابر ضربه دارد و به راحتی ورقه و کنده می شود. برخلاف سیلندرهای سنتی که اغلب قابل ترمیم و پوشش دهی مجدد با کروم بودند، سیلندرهای سرامیکی چنانچه از نقاط پایه ای کنده شوند، قابل ترمیم نخواهند بود. در این شرایط تنها می توان لایه سرامیکی را به طور کامل لایه برداری کرد و لایه جدیدی ساخت. در مورد تخریب های جزیی نیز می توان آنها را با اپوکسی همساز ترمیم کرد تا گسترش نیابند. یکی دیگر از مزایای سیلندر LEC، امکان اعمال پوشش های یک دست چندلایه و ضد زنگ در زیر لایه سرامیک است که سیلندر را در برابر خوردگی بسیار مقاوم تر می سازد.
در مورد فرآیند پوشش دهی، سازنده سیلندر LEC، به اطلاعاتی مانند وزن مخصوص یا ضخامت لایه پوشش خشک شده و نوع فرایند نیاز دارد. همچنین مشخصات فنی مرکب- درصد مواد جامد، اندازه پیگمنت، نوع حامل – و بستر چاپی می توانند در انتخاب نوع حکاکی موثر باشند. در روش های چاپی فلکسو و افست – گراور، به 19 تا 23 درصد بازدهی رسوب نیاز است. نورد آنیلوس در فلکسو باید ظرفیت حجم (BillIon Cubic Microns-BCM) بیشتری داشته باشد. بازدهی رسوب در چاپ گراور مستقیم 40 تا 45 درصد است، بنابراین آنیلوکس آن به ظرفیت حجمی کمتری نسبت به فلکسو نیاز دارد. خواص رطوبت پذیری بستر چاپی نیز برای انتخاب نوع حکاکی آنیلوکس مهم است. برای مثال، انتخاب زاویه 30 درجه برای حفره های آنیلوکس موجب کاهش سفیدک زدن فیلم چاپی می شود. (شکل3 pinoling )
نگهداری و تعمیرات سیلندرLEC
زمانی از سیلندرهای LEC در فرایند گراور استفاده شود، نگهداری آن بسیار اهمیت بیشتری می یابد. همواره از روکش های محافظ برای آنیلوکس استفاده کنید و سیلندر آن را از ضربه در امان بدارید. همان طور که گفته شد، سرامیک، برخلاف مقاومت زیاد خود در برابر خوردگی، مقاومت بسیار پایینی دارد. برای شست و شوی سیلندرLEC از برس های استیل ضد زنگ مخصوص آنیلوکس استفاده کنید. هیچ گاه از برس های برنجی برای تمیزکاری سطح آنیلوکس سرامیکی استفاده نکنید. همه سیستم های شست و شوی پس از چاپ، مانند پاشش با فشار سودا یا دیگر شوینده ها، تانک های شست و شوی و سیستم های چرخشی اتوماتیک قابل استفاده هستند. اما همواره بهتر است پیش از به کارگیری این سیستم ها با تامین کننده سیلندر خود، در مورد مواد شیمیایی، شوینده ها و پارامترهای آن مشاوره کنید. پس از شست و شوی سیلندرها در هر گونه سیستم پایه آب، همیشه آن ها را بلافاصله به طور کامل خشک کنید. برای این منظور می توانید از چرخش دوار سیلندر، یا الکل یا کمپرس هوای بدون چربی استفاده کنید.